production of a bronze figure
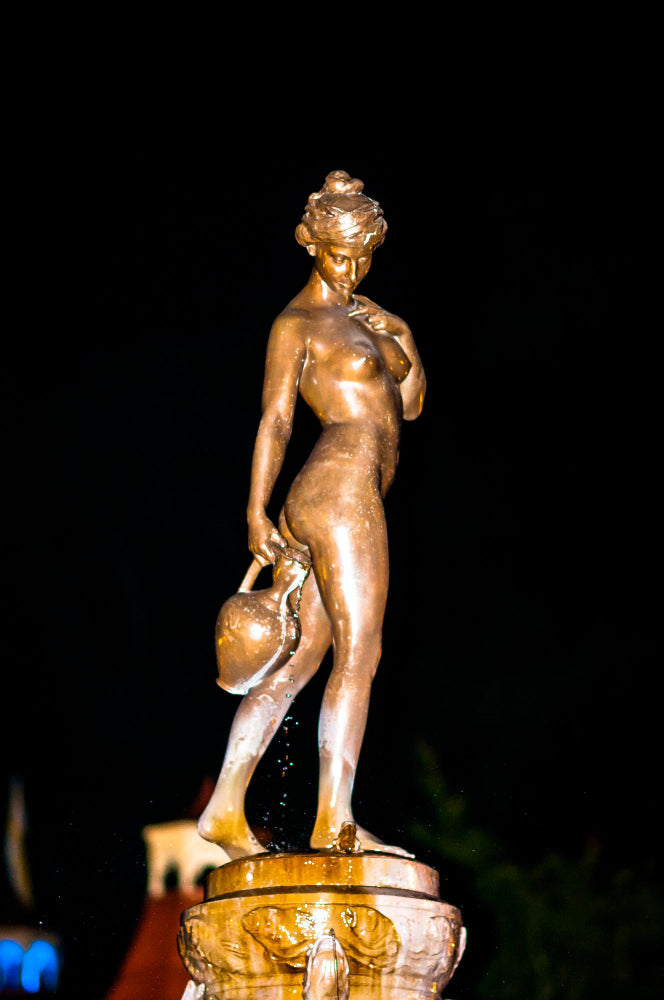

Bronze
We live in an age in which non-recurring raw materials are becoming increasingly important and are therefore becoming increasingly expensive. This includes bronze. But what exactly is bronze? Bronze is the oldest alloy of all. It consists of 10% tin and 90% copper in the casting sector for artist bronzes.
The first commercial production of bronze dates back to around 2500-2000 BC and is believed to have begun in the Near East. The Bronze Age is etched into the history of humanity and gave rise to an age of metal objects such as weapons, tools and equipment in Central Europe around 2200-800 BC.
The properties of bronze were highly valued and the material could easily be melted down and reprocessed.
How is a bronze figure created?
- The first thing that comes from this is the idea. Our artists put it on a sheet of paper or model it into a figure from a lump of clay or wax. This is the first step towards creating our bronze sculpture and serves as a template for the subsequent silicone negative. An elaborately designed clay or wax model is then created through artistic fine work.
- The finished clay/wax model is now covered in several layers of silicone until it is completely covered. After the silicone has hardened, we now have an almost complete negative for our later bronze sculpture. The hardened silicone coating is now removed from the clay/wax model and provided with plaster support shells to hold the mold for the subsequent wax casting.
- The silicone negative is then carefully filled with a special wax to form the wax positive. In several steps, the mold is carefully filled with mm layers of wax, which determine the later thickness of the cast. This requires extreme skill, as no air bubbles must form when the wax is first poured into the mold, as they determine the later surface of the model. Once the wax has completely hardened, the wax positive can be removed. Any fine and detailed work, such as removing seams from the silicone negative, is retouched.
- Before the wax model is given a fireclay coating (more on that in a moment), it must be prepared for this. The wax model is now provided with pouring and ventilation channels to allow excess air to escape during the actual bronze casting and to provide the entrance for the subsequent bronze casting.
- The wax model is now embedded in fireclay. The wax model is completely embedded in plaster and fireclay, which is used in a special vacuum process to create a pore-free surface for the subsequent bronze casting. The models, which have now been embedded in fireclay, are fired in a specially designed drying oven for several days until the wax has flowed out of the fireclay molds without leaving any residue or has melted out - the lost wax process. What remains is the desired cavity for the subsequent liquid bronze.
- Now the glowing hot liquid bronze can finally be poured into the desired fireclay mold. The previously installed ventilation channels are now used and allow excess air to escape and help the bronze casting to cool down. After the bronze casting has cooled, the bronze blank can now be freed from its fireclay coating by smashing it. A bronze figure is now almost finished and its mold is completely destroyed. To create this sculpture again, the entire procedure must begin with the wax model. This is followed by brushing and polishing to completely remove the fireclay from the bronze casting. The previously installed pouring and ventilation devices are removed and any unevenness on the surface is polished out. The sculpture is now prepared for subsequent patination.
- Patination gives the sculpture its final appearance. The surface of the bronze
is subjected to an artificially induced aging process using chemical processes, which the bronze actually needs over decades. The color of the bronze becomes darker over the years. This is again a complex process that is achieved through oxidation and deoxidation. Chemicals such as hydrogen peroxide, copper and iron oxide, as well as potassium sulfide are used. After multiple applications and drying processes in specially designed drying ovens, individual effects and colors are created. This process requires a high degree of experience and expertise. - This further process gives each sculpture its own special touch and uniqueness. Finally, the sculpture is preserved using a very thin layer of wax under the influence of heat and can then be mounted on the marble base provided for you.
- Now a bronze sculpture, created entirely by hand and with a great deal of artistic understanding and skill, as well as decades of experience, is waiting for a new owner in our house WRIGHT MAGNIFICENT SCULPTURES. Many years of experience make our products timeless works of art.
We are also happy to offer you custom-made pieces. We have a large selection and variety of sculptures based on the great masters of all eras.
Are you looking for a specific sculpture and can't find it?
We are there for you every day at 0172-7424682.